ซีเมนต์คาร์ไบด์เป็นวัสดุแข็งชนิดหนึ่งที่ประกอบด้วยสารประกอบโลหะแข็งที่ทนไฟและโลหะยึดติด ซึ่งผลิตขึ้นจากผงโลหะและมีความทนทานต่อการสึกหรอสูงและมีความเหนียวในระดับหนึ่ง เนื่องจากประสิทธิภาพที่ยอดเยี่ยม ซีเมนต์คาร์ไบด์จึงใช้กันอย่างแพร่หลายในการตัด ชิ้นส่วนที่ทนทานต่อการสึกหรอ การทำเหมือง การขุดเจาะทางธรณีวิทยา การขุดน้ำมัน ชิ้นส่วนเครื่องจักร และสาขาอื่นๆ
กระบวนการผลิตซีเมนต์คาร์ไบด์ประกอบด้วยกระบวนการหลัก 3 ขั้นตอน ได้แก่ การเตรียมส่วนผสม การขึ้นรูปด้วยแม่พิมพ์ และการเผาผนึก แล้วกระบวนการนี้คืออะไร?
กระบวนการและหลักการแบตช์
ชั่งน้ำหนักวัตถุดิบที่ต้องการ (ผงทังสเตนคาร์ไบด์ ผงโคบอลต์ ผงวาเนเดียมคาร์ไบด์ ผงโครเมียมคาร์ไบด์ และสารเติมแต่งจำนวนเล็กน้อย) ผสมตามตารางสูตร ใส่ในเครื่องบดลูกกลิ้งหรือเครื่องผสมเพื่อบดวัตถุดิบต่างๆ เป็นเวลา 40-70 ชั่วโมง เติมขี้ผึ้ง 2% กลั่นและกระจายวัตถุดิบในเครื่องบดลูกกลิ้งให้สม่ำเสมอ จากนั้นทำส่วนผสมที่มีองค์ประกอบและขนาดอนุภาคตามข้อกำหนดผ่านการทำให้แห้งแบบพ่นหรือผสมด้วยมือและการคัดกรองแบบสั่น เพื่อตอบสนองความต้องการในการกดและการเผาผนึก หลังจากการกดและการเผาผนึก แผ่นคาร์ไบด์ซีเมนต์จะถูกปล่อยออกและบรรจุหีบห่อหลังจากการตรวจสอบคุณภาพ
ส่วนผสมรวม
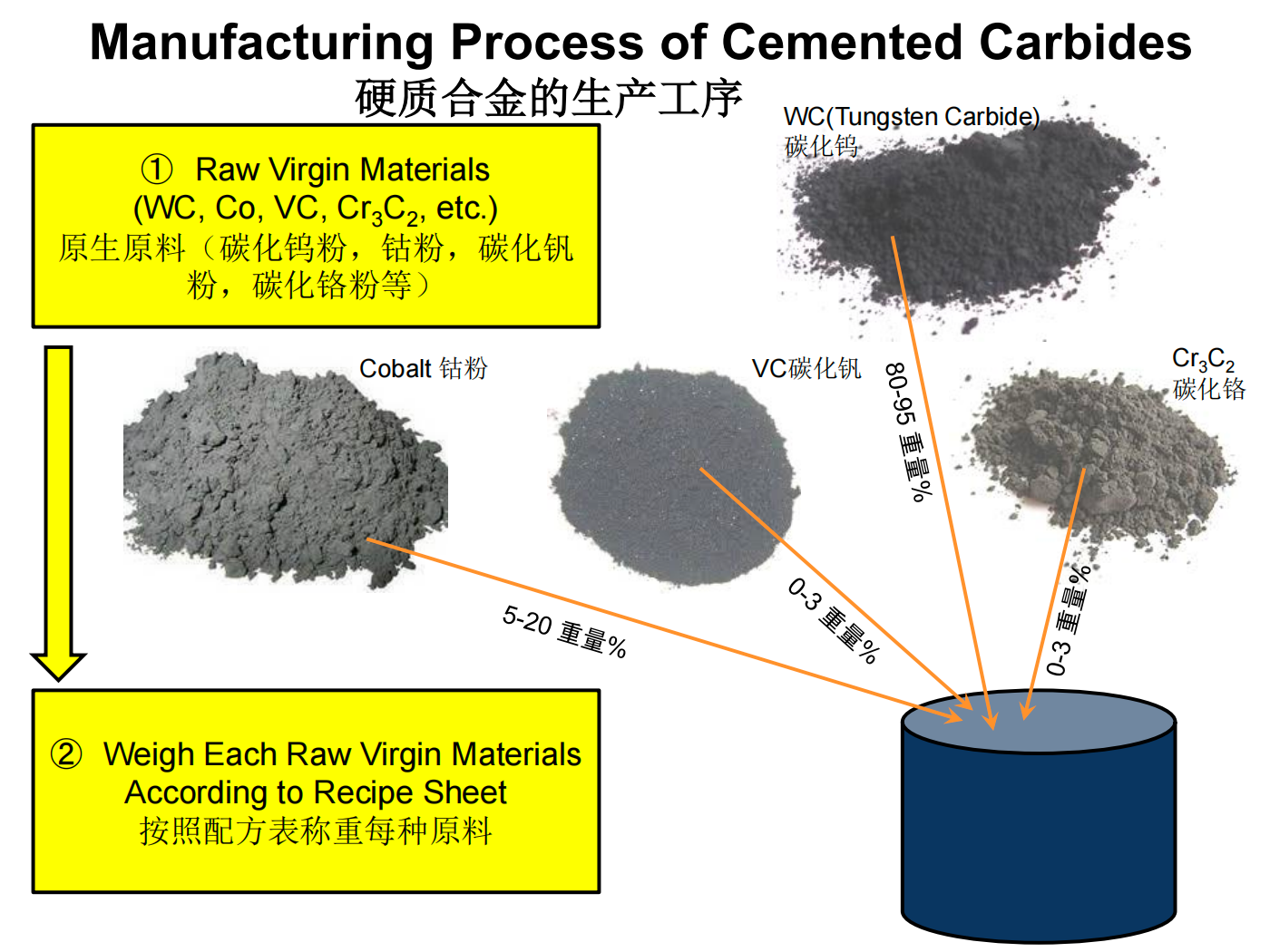
การบดแบบเปียก
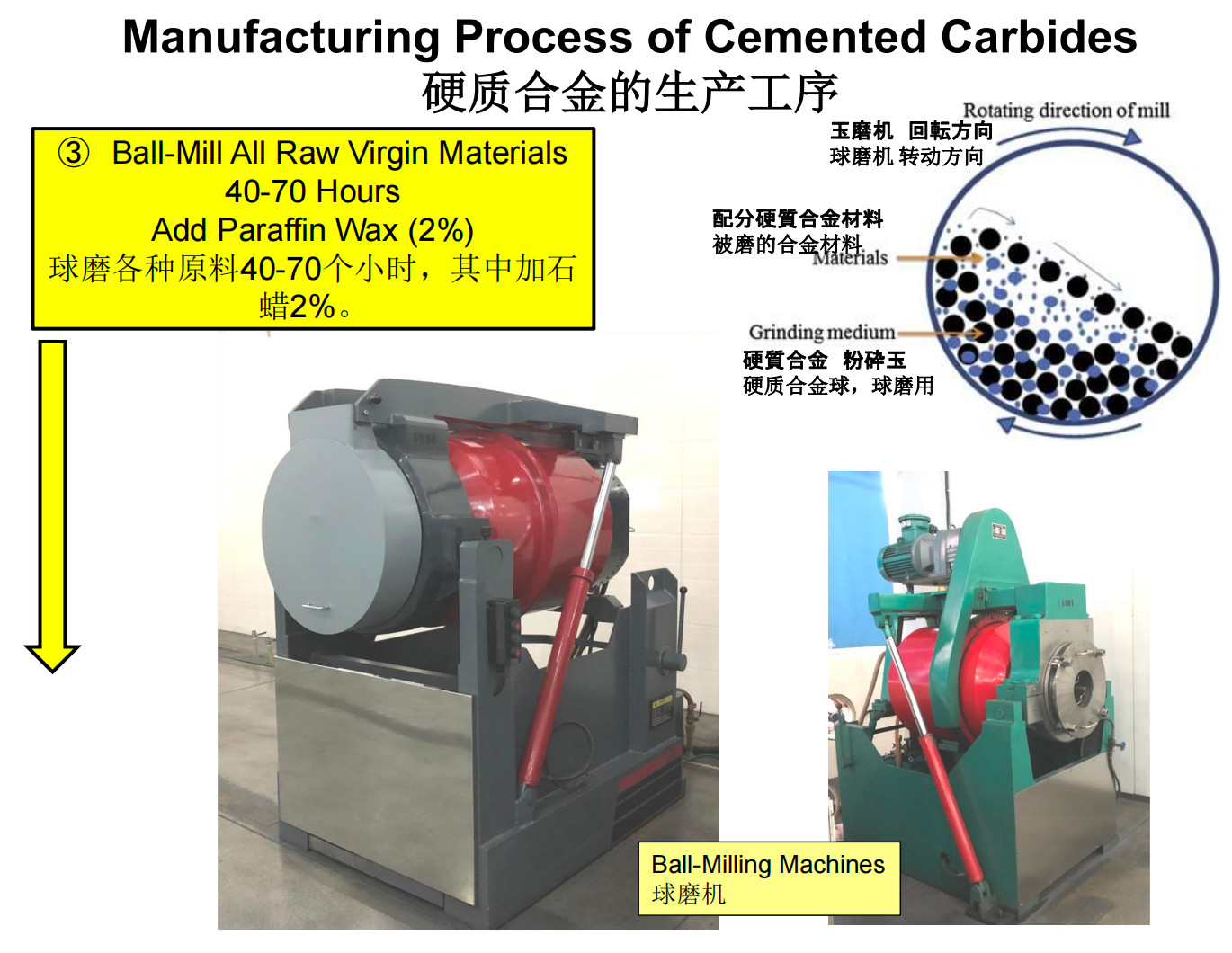
การแทรกซึมของกาว การทำให้แห้ง และการทำให้เป็นเม็ด
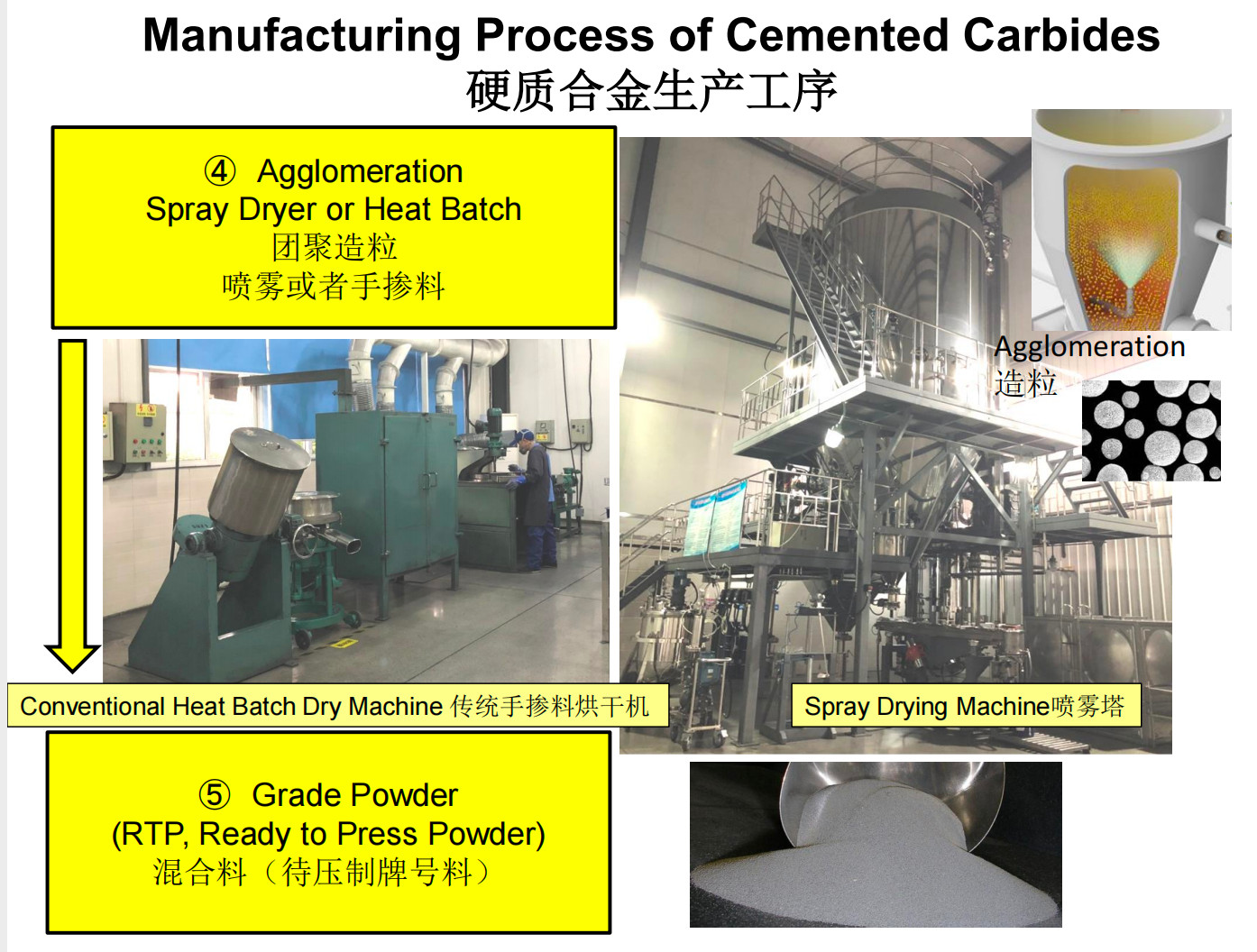
การขึ้นรูปด้วยแม่พิมพ์
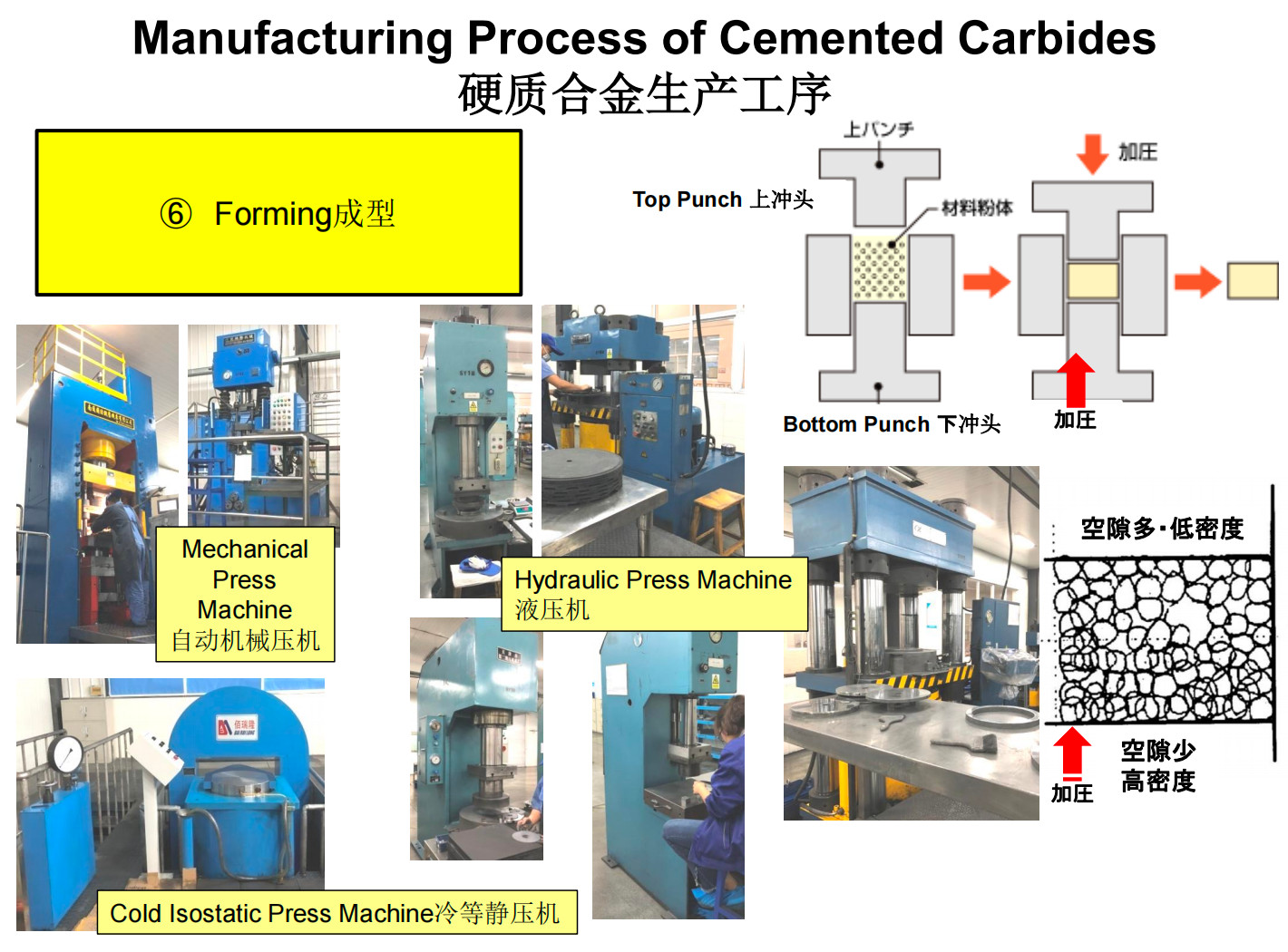
ซินเตอร์
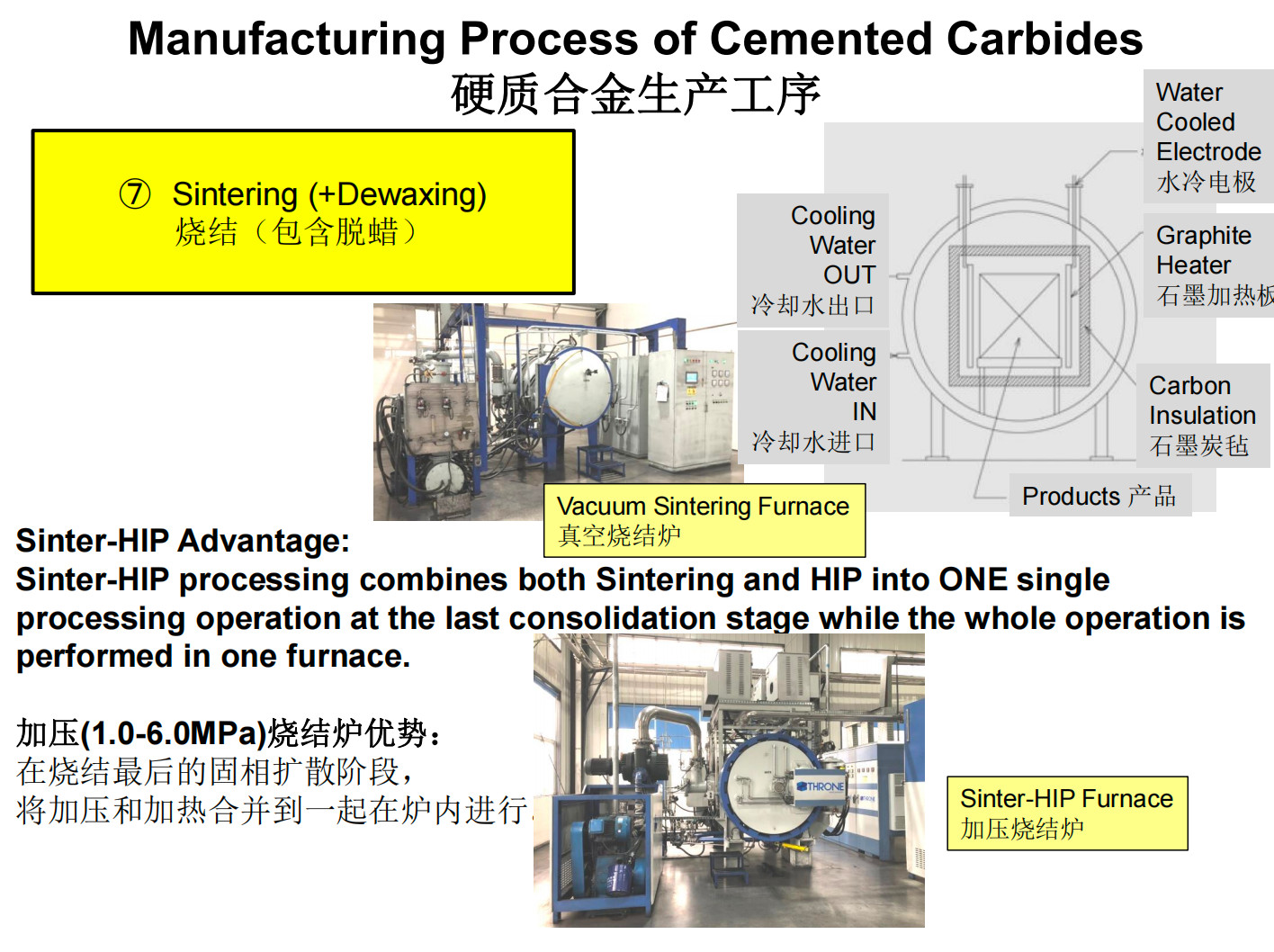
คาร์ไบด์ซีเมนต์เปล่า
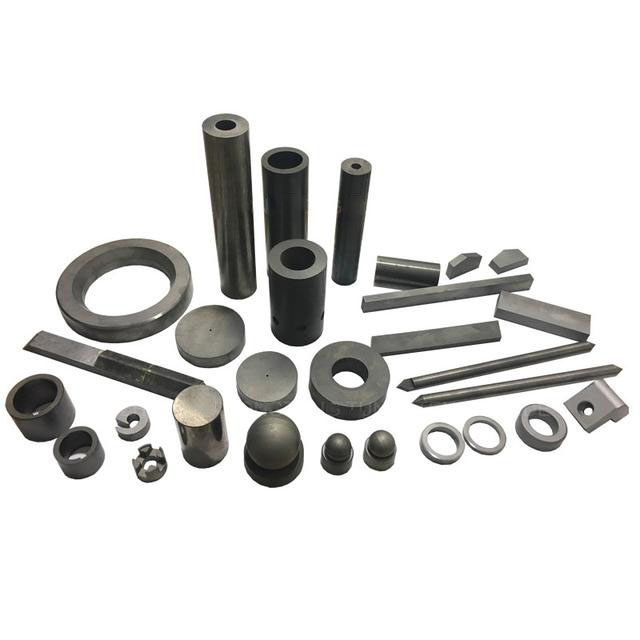
การตรวจสอบ
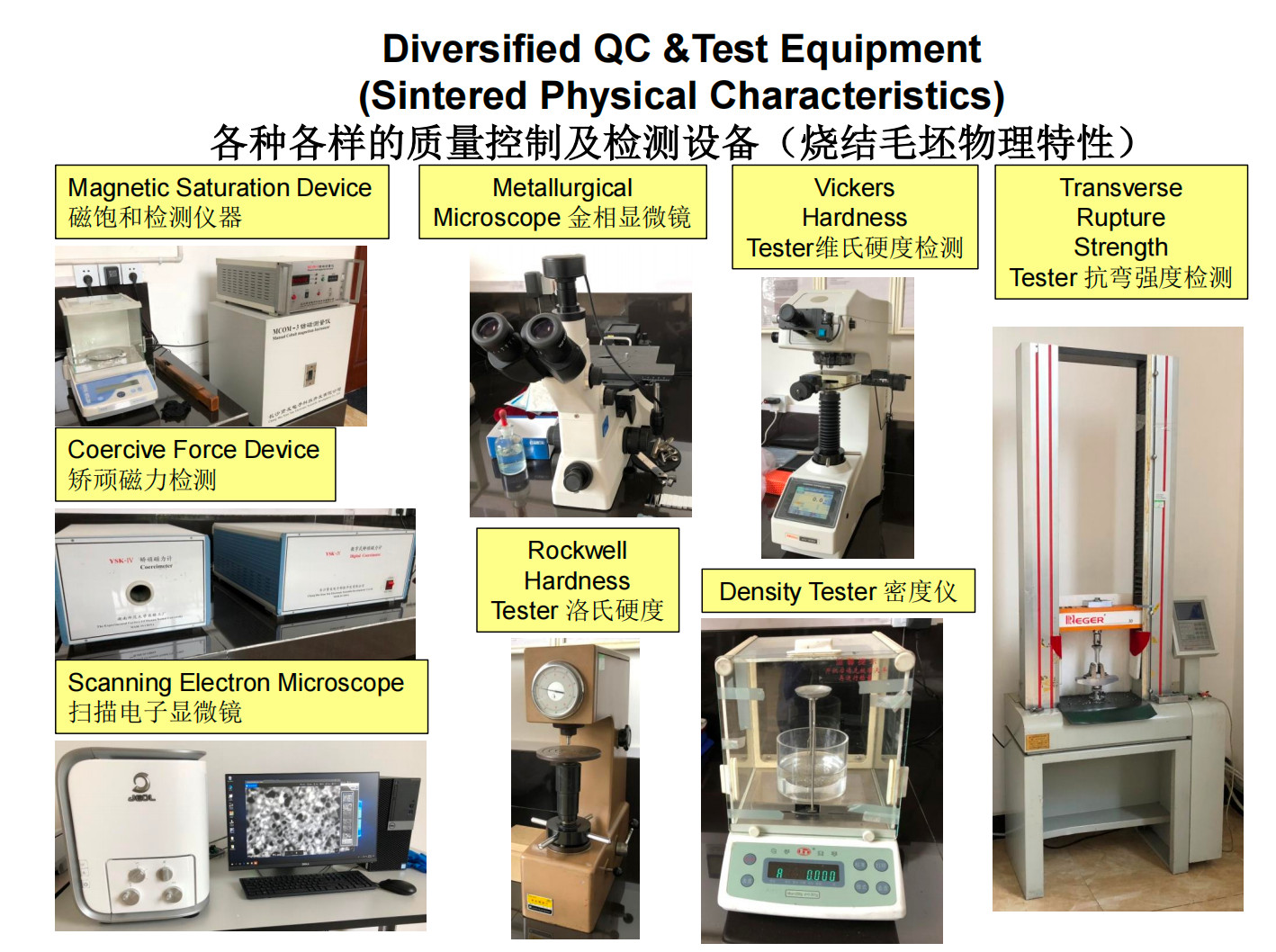
สูญญากาศคืออะไร?
สุญญากาศเช่นนี้คือบริเวณที่มีความดันก๊าซน้อยกว่าความดันบรรยากาศมาก นักฟิสิกส์มักหารือถึงผลการทดสอบในอุดมคติในสภาวะสุญญากาศสัมบูรณ์ ซึ่งบางครั้งเรียกว่าสุญญากาศหรืออวกาศอิสระ จากนั้นจึงใช้สุญญากาศบางส่วนเพื่อแสดงถึงสุญญากาศที่ไม่สมบูรณ์ในห้องปฏิบัติการหรือในอวกาศ ในทางกลับกัน ในทางวิศวกรรมและการประยุกต์ใช้ทางกายภาพ เราหมายถึงอวกาศใดๆ ก็ตามที่มีความดันต่ำกว่าความดันบรรยากาศ
ข้อบกพร่อง/อุบัติเหตุทั่วไปในการผลิตผลิตภัณฑ์คาร์ไบด์ซีเมนต์
หากย้อนกลับไปที่สาเหตุหลัก ข้อบกพร่อง/อุบัติเหตุจากการผลิตคาร์ไบด์ซีเมนต์ที่พบบ่อยที่สุดสามารถแบ่งออกได้เป็นสี่ประเภท:
ข้อบกพร่องของส่วนประกอบ (เฟส ETA ปรากฏขึ้น กลุ่มอนุภาคขนาดใหญ่ก่อตัว รอยแตกจากการอัดผง)
ข้อบกพร่องในการประมวลผล (รอยแตกจากการเชื่อม รอยแตกจากการตัดลวด รอยแตกจากความร้อน)
อุบัติเหตุทางสิ่งแวดล้อม (การกัดกร่อน การสึกกร่อน ฯลฯ)
อุบัติเหตุทางกล (เช่น การชนแบบเปราะ การสึกหรอ ความเสียหายจากความล้า ฯลฯ)
เวลาโพสต์ : 27 ก.ค. 2565